In regulated industries like medical device manufacturing, ensuring product quality and compliance with stringent regulatory standards is paramount; within the realm of process validation, Installation Qualification (IQ) serves as a critical first step, particularly for medical device manufacturers. In this blog post, we’ll explore the significance of IQ in the context of medical device manufacturing, its key components, and best practices for implementation.
We have already been discussing about process validation, especially for specific processes such as cleaning, sterilization, reprocessing etc. Within this article, we will mainly discuss about Installation Qualification, on of the main step of the IQ/OQ/PQ installation techniques.
What is Installation Qualification (IQ)?
Installation Qualification, or IQ, is a foundational phase of process validation where equipment, systems, and facilities are verified to ensure they are installed correctly and in accordance with predetermined specifications and requirements. For medical device manufacturers, IQ is essential to establishing the integrity and reliability of manufacturing processes, ensuring adherence to regulatory standards such as those set forth by the U.S. Food and Drug Administration (FDA).
Significance of IQ in Medical Device Manufacturing
In the highly regulated environment of medical device manufacturing, adherence to quality standards and regulatory requirements is non-negotiable. IQ serves as a critical control point to verify that equipment and systems are installed correctly and capable of meeting the stringent quality and safety requirements of medical device manufacturing processes. By conducting IQ, medical device manufacturers can proactively identify and address any installation issues or discrepancies, laying the groundwork for subsequent stages of process validation and ensuring product quality and patient safety.
Key Components of Installation Qualification
- Documentation Review: Medical device manufacturers begin the IQ process with a thorough review of equipment specifications, installation instructions, and relevant documentation to ensure compliance with FDA regulations and industry standards, such as ISO 13485.
- Equipment Verification: Physical verification of equipment and components is conducted to confirm that they have been installed in the correct location, according to the manufacturer’s specifications, and in compliance with engineering drawings and diagrams.
- Calibration and Qualification: Instruments, sensors, and measurement devices are calibrated and qualified to ensure accuracy and reliability in monitoring and controlling critical process parameters, such as temperature, pressure, and humidity.
- Functional Testing: Functional testing is performed to verify that equipment and systems operate as intended and meet performance criteria specified in user requirements and functional specifications. This includes testing for functionality, accuracy, and reliability under simulated operating conditions.
- Environmental Conditions: Environmental conditions within the manufacturing environment, such as temperature, humidity, and cleanliness, are monitored and documented to ensure they are within acceptable limits for the operation of equipment and processes, as required by FDA regulations.
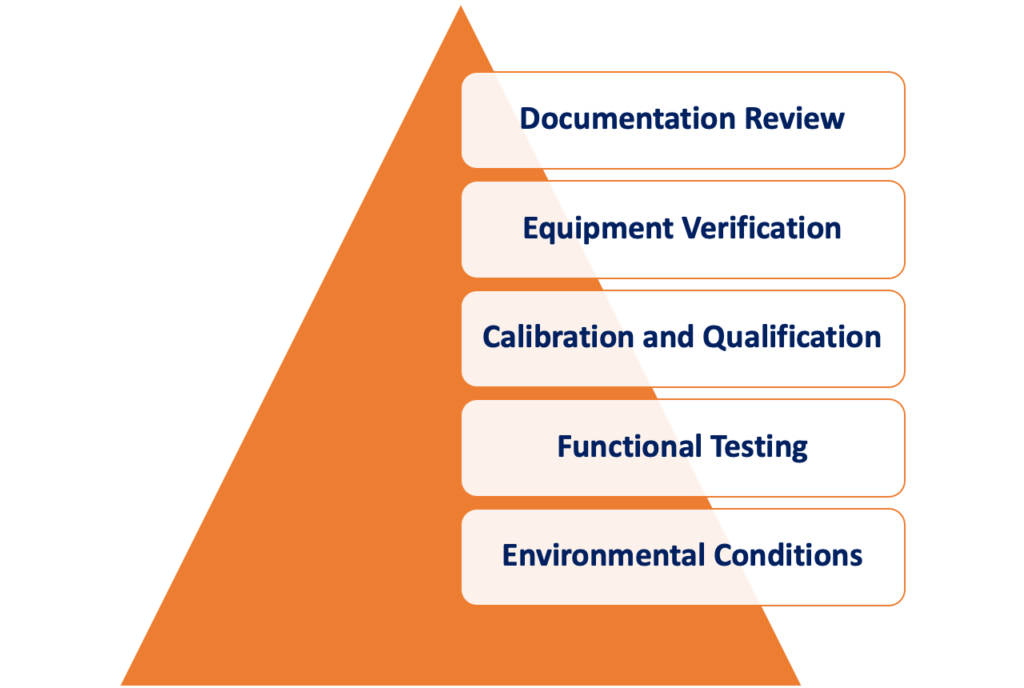
Best Practices for IQ Implementation in Medical Device Manufacturing
- Establish Clear Protocols: Medical device manufacturers should develop standardized protocols and procedures for conducting IQ, including checklists, forms, and documentation templates, to ensure consistency and compliance with FDA regulations and industry standards.
- Conduct Risk Assessment: Prioritize critical equipment and systems based on their impact on product quality, patient safety, and regulatory compliance. Conduct risk assessments to identify potential hazards and mitigate risks associated with installation issues.
- Involve Cross-Functional Teams: Collaborate with cross-functional teams, including engineering, quality assurance, regulatory affairs, and operations, to ensure comprehensive coverage and expertise during IQ activities.
- Document Everything: Maintain detailed records of IQ activities, including equipment specifications, installation records, test results, deviations, and corrective actions. Documentation should be thorough, accurate, and readily accessible for FDA inspections and audits.
- Perform Requalification: Periodic requalification of equipment and systems is essential to ensure continued compliance with FDA regulations and changes in operational conditions over time. Develop a schedule for requalification based on risk assessment and industry best practices.
Subscribe to 4EasyReg Newsletter
4EasyReg is an online platform dedicated to Quality & Regulatory matters within the medical device industry. Have a look to all the services that we provide: we are very transparent in the pricing associated to these consulting services.
Within our WebShop, a wide range of procedures, templates, checklists are available, all of them focused on regulatory topics for medical device compliance to applicable regulations. Within the webshop, a dedicated section related to cybersecurity and compliance to ISO 27001 for medical device organizations is also present.
As one of the leading online platforms in the medical device sector, 4EasyReg offers extensive support for regulatory compliance. Our services cover a wide range of topics, from EU MDR & IVDR to ISO 13485, encompassing risk management, biocompatibility, usability, software verification and validation, and assistance in preparing technical documentation for MDR compliance.
Do not hesitate to subscribe to our Newsletter!